Production plants need practical help for operational everyday life. Different information is needed to support different functions. The best result and added value are achieved through cooperation.
A digital system alone does not maximize the targeted savings. When the decision to digitize the operation has been made, let’s get down to concrete things. So how do the current meters support different functions?
At their best, digital systems can produce clear and reliable observations for experts to analyze. The simplest procedures can be automated on a rule-based basis, and as the system develops, machine learning can also be added and thus make maintenance work more efficient. By reducing routine maintenance tasks, work can be allocated to maintaining operational reliability.
Utilizing the information already collected in the automation systems is usually the first step. By extending data collection to smart devices, the quality and coverage of usable data can be increased. However, the best result and added value is achieved by combining the analytics features developed by device manufacturers into the overall system. By increasing sensors and virtual measurements, the information obtained from devices and processes can be supplemented even further. In this way, the unambiguous information produced by the system can be directly automated, for example, into a maintenance work schedule, and thus make operations more efficient. Of course, experts are still needed to analyze more demanding situations.
The service provider helps improve maintenance and process efficiency
When you’re in a hurry, the challenge is to find enough time to properly use the system and plan what to do. In this case, the alternative is to rely on the system and process supplier’s service contract. At best, the service provider is a good sparring partner who provides help in planning maintenance work and doing everyday things. They know the equipment and are therefore able to effectively find the areas where the failure has already started but has not yet had time to break the equipment.
That’s why it’s worth involving the service provider in doing it regularly. Moving from boring and long reports to a clear to-do list with responsible persons enables tangible results. At the beginning, it is good to go through the maintenance and failure history from a longer period and learn from things that have already happened. In this way, we and other suppliers are better able to customize and develop the system and learn more quickly the operation of the customer’s facility and the related challenges. Together, let’s move from calendar-based maintenance to need-based maintenance.
When digitizing operations, you should start by defining operational challenges and goals and finding out what kind of information is available in the systems. Service providers, on the other hand, help to develop operating methods. With clear data-based changes made in cooperation with client companies, the results of operational metrics improve.
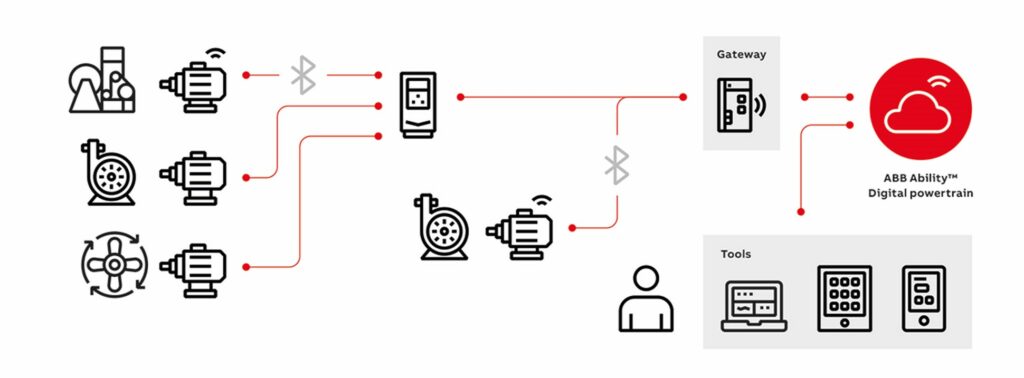
In EU IoT-NGIN project, ABB has developed and implemented solutions to improve condition monitoring for powertrains. The laboratory setup includes several electric motors and frequency converters equipped with tens of sensors. Sensor and device data is collected and structured using Semantic Twin approach. Finally, data is visualized and analyzed to create digital services for maintenance operators of powertrains, for example. The implemented laboratory setup can be used as framework i.e., to improve analytics solutions and therefore create added value for maintenance operators and customers.